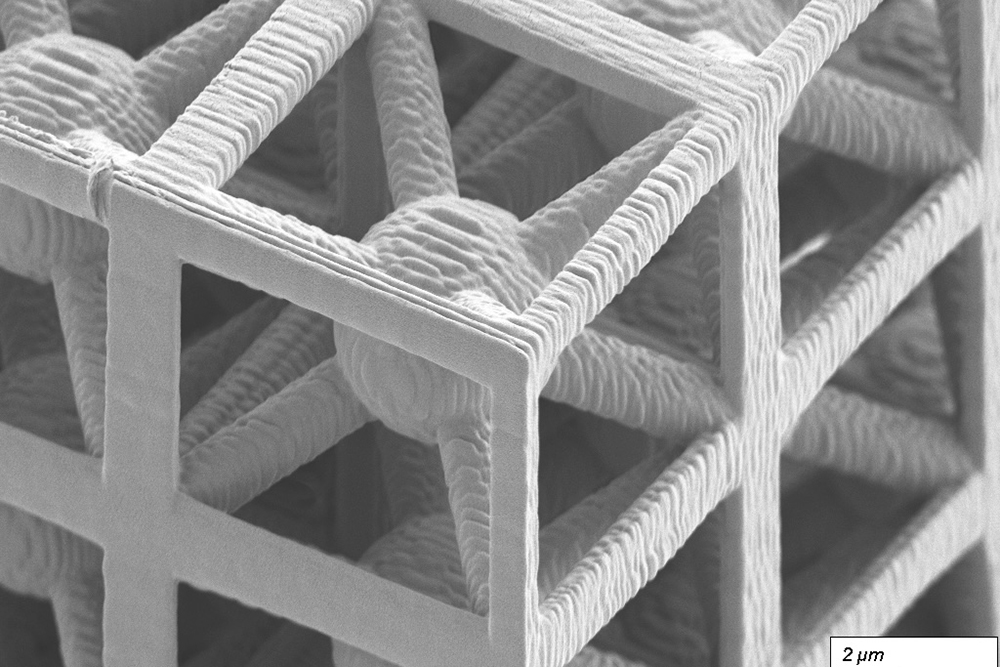
Acoustic metamaterials — architected materials that have tailored geometries designed to control the propagation of acoustic or elastic waves through a medium — have been studied extensively through computational and theoretical methods. Physical realizations of these materials to date have been restricted to large sizes and low frequencies.
“The multifunctionality of metamaterials — being simultaneously lightweight and strong while having tunable acoustic properties — make them great candidates for use in extreme-condition engineering applications,” explains Carlos Portela, the Robert N. Noyce Career Development Chair and assistant professor of mechanical engineering at MIT. “But challenges in miniaturizing and characterizing acoustic metamaterials at high frequencies have hindered progress towards realizing advanced materials that have ultrasonic-wave control capabilities.”
A new study coauthored by Portela; Rachel Sun, Jet Lem, and Yun Kai of the MIT Department of Mechanical Engineering (MechE); and Washington DeLima of the U.S. Department of Energy Kansas City National Security Campus presents a design framework for controlling ultrasound wave propagation in microscopic acoustic metamaterials. A paper on the work, “Tailored Ultrasound Propagation in Microscale Metamaterials via Inertia Design,” was recently published in the journal Science Advances.
“Our work proposes a design framework based on precisely positioning microscale spheres to tune how ultrasound waves travel through 3D microscale metamaterials,” says Portela. “Specifically, we investigate how placing microscopic spherical masses within a metamaterial lattice affect how fast ultrasound waves travel throughout, ultimately leading to wave guiding or focusing responses.”
Through nondestructive, high-throughput laser-ultrasonics characterization, the team experimentally demonstrates tunable elastic-wave velocities within microscale materials. They use the varied wave velocities to spatially and temporally tune wave propagation in microscale materials, also demonstrating an acoustic demultiplexer (a device that separates one acoustic signal into multiple output signals). The work paves the way for microscale devices and components that could be useful for ultrasound imaging or information transmission via ultrasound.
“Using simple geometrical changes, this design framework expands the tunable dynamic property space of metamaterials, enabling straightforward design and fabrication of microscale acoustic metamaterials and devices,” says Portela.
The research also advances experimental capabilities, including fabrication and characterization, of microscale acoustic metamaterials toward application in medical ultrasound and mechanical computing applications, and underscores the underlying mechanics of ultrasound wave propagation in metamaterials, tuning dynamic properties via simple geometric changes and describing these changes as a function of changes in mass and stiffness. More importantly, the framework is amenable to other fabrication techniques beyond the microscale, requiring merely a single constituent material and one base 3D geometry to attain largely tunable properties.
“The beauty of this framework is that it fundamentally links physical material properties to geometric features. By placing spherical masses on a spring-like lattice scaffold, we could create direct analogies for how mass affects quasi-static stiffness and dynamic wave velocity,” says Sun, first author of the study. “I realized that we could obtain hundreds of different designs and corresponding material properties regardless of whether we vibrated or slowly compressed the materials.”